Description
The D-040 L Combination Air Valve has the features of both an air release valve and an air & vacuum valve in a single body. This air valve is specifically designed to operate with liquids containing small suspended solids.
The air release component is designed to automatically release small pockets of air to the atmosphere as they accumulate along a pipeline or piping system when it is full and operating under pressure.
The air & vacuum component is designed to automatically discharge or admit large volumes of air during the filling or draining of a pipeline or piping system. This air valve will open to relieve negative pressures whenever water column separation occurs. The valve’s unique design enables the separation of the liquid from the sealing mechanism and assures optimum working conditions.
Applications
- Water transmission lines.
Operation
The air & vacuum component, with the large orifice, discharges air at high flow rates during the filling of the system and admits air into the system at high flow rates during its drainage and at water column separation.
High velocity air will not blow the float shut. Water will lift the float, which seals the valve.
At any time during system operation, should internal pressure of the system fall below atmospheric pressure, air will enter the system. The smooth discharge of air reduces pressure surges and other destructive phenomena.
The intake of air in response to negative pressure protects the system from destructive vacuum conditions and prevents damage caused by water column separation. Air entry is essential to efficiently drain the system.
The air release component releases entrapped air in pressurized systems.
Without air valves, pockets of accumulated air may cause the following hydraulic disturbances:
- Restriction of effective flow due to a reduction of the flow area. In extreme cases this will cause complete flow stoppage.
- Obstruction of efficient hydraulic transmission due to air flow disturbances.
- Acceleration of cavitation damages.
- Increase in pressure transients and surges.
- Internal corrosion of pipes, fittings and accessories.
- Dangerous high-energy bursts of compressed air.
- Inaccuracies in flow metering.
As the system starts to fill with liquid, the valve functions according to the following stages:
1. Air/gas is discharged by the air valve.
2. When the liquid enters the air valve, the float buoys up, pushing the sealing mechanism to its sealing position.
3. The entrapped air is confined in a pocket between the liquid
and the sealing mechanism. The air pressure is equal to the system pressure.
4. Increases in system pressure compress the trapped air. The remaining air gap enables the separation of the liquid from the sealing mechanism.
5. Entrapped air/gas, accumulating at peaks and along the system, rises to the top of the air valve and displaces the liquid in the air valve body.
6. When the liquid level is lowered to a point where the float is no longer buoyant, the float drops, unsealing the rolling seal. The air release orifice opens and allows part of the air that accumulated in the valve to be released to the atmosphere.
7. Liquid enters the valve. The float rises, pushing the rolling seal to its sealing position. The remaining air gap prevents the solids- laden liquid from reaching the sealing mechanism.
When internal pressure falls below atmospheric pressure (negative pressure):
1. The float will immediately drop down, opening the air & vacuum and air release orifices.
2. Air will enter the system.
Main Features
- Working pressure range: Polypropylene: 0.02 - 10 bar
St.St. SAE 316 / Duplex / Reinforced Nylon / PVDF: 0.05 - 16 bar - Testing pressure: 1.5 times the maximum working pressure
- Maximum working temperature: 60°C.
- Maximum intermittent temperature: 90°C.
- Builds an air gap that separates the liquids with suspended particles from the sealing mechanism.
- Dynamic design allows for high capacity air discharge while preventing premature closure.
- Lightweight, small dimensions, simple and reliable structure.
- The discharge outlet enables the connection of a vent pipe
- The large size of the automatic air release orifice relative to the air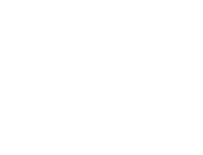
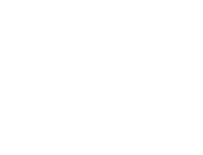
D-040 L
valve body:
• Releases air at high flow rates.
• Lessens the danger of its obstruction by debris.
• The valve’s rolling seal mechanism design is less sensitive to different pressures than a direct float seal, thus enabling a one size orifice for a wide pressure range (up to 16 bar).
- The body is made of high-strength materials and all operating parts are made of specially selected, corrosion- resistant materials.
- Due to its light weight, the valve may be installed on plastic piping systems, as well as other lightweight piping systems.
Valve Selection
- Available in male threaded sizes: 1/2”, 3/4”, 1”, 2” - BSP / NPT and 2” flanged
- The D-040 L series air valve is available as:
D040 L-V -With a one-way, out-only attachment, allows air
discharge only, prevents air intake (all models).
D-040 L-I -With a vacuum breaker, in-only attachment, allows air intake only, not allowing air discharge (D-040 L 2”only).
D-040 L-NS -With a non-slam, discharge-throttling attachment, allows full air intake, throttles air discharge (D-040 L 2”only).
Note
For best suitability, it is recommended to send the fluid chemical properties along with the valve request.
Upon ordering, please specify: model, size, working pressure, thread and flange standard and type of liquid.
A.R.I. FLOW CONTROL ACCESSORIES Ltd. reserves the right to make product changes without prior notice. To insure receiving updated information on parts specifications, please call the export dept. at the A.R.I. factory. A.R.I. FLOW CONTROL ACCESSORIES Ltd. shall not be held liable for any errors. All rights reserved.